FALCON USER’S GUIDE Hold-on-pad operations, enabled by the launch vehicle’s all-liquid propulsion architecture and autonomous countdown sequence, significantly reduce risks associated with engine start-up failures and underperformance. By employing multiple first-stage engines, SpaceX offers the world’s first evolved expendable launch vehicle (EELV)- class system with engine-out capability through much of first-stage flight. System-level vehicle management software controls the shutdown of engines in response to off-nominal engine indications. Although the likelihood of catastrophic engine failure is low, and failing engines are designed to be shut down prior to a catastrophic failure, each engine is housed within its own metal bay to isolate it from neighboring engines. The second-stage Merlin Vacuum engine uses a fixed, non-deploying expansion nozzle, eliminating potential failure modes in nozzle extension. 1.5.2 AVIONICS Falcon launch vehicle avionics, and guidance, navigation and control systems use a fault-tolerant architecture that provides full vehicle single-fault tolerance and uses modern computing and networking technology to improve performance and reliability. The fault tolerance is achieved either by isolating compartments within avionics boxes or by using triplicated units of specific components. Both the first and second stages host their own multiple redundant lithium-ion batteries to minimize the complexity of the electrical interface. 1.5.3 STAGING ARCHITECTURE AND DESIGN The two-stage Falcon 9 architecture was selected to minimize the number of stage separation events, eliminating potential failure modes associated with third- and fourth-stage separations, as well as potential engine deployment and ignition failure modes in the third and fourth stages. Falcon Heavy uses the same stage architecture as Falcon 9 with the addition of two separating side cores. The Falcon second-stage and Falcon Heavy side-boosters restraint, release, and separation systems use pneumatic devices that provide low-shock release and positive force separation over a comparatively long stroke. The pneumatic system allows for acceptance and functional testing of the actual flight hardware, which is not possible with a traditional explosives-based separation system. For each Falcon launch vehicle, SpaceX performs an exhaustive series of tests from the component to the vehicle system level. The test program includes component-level flight acceptance and workmanship testing, structures load and proof testing, flight system and propulsion subsystem-level testing, full first- and second-stage testing up to full system testing (including first- and second-stage static fire testing), as well as a static fire test on the launch pad. In addition to testing environmental extremes (plus margin), flight critical and workmanship sensitive hardware are tested to account for off-nominal conditions. For example, stage separation tests are performed for off-nominal cases with respect to geometrical misalignment, anomalous timing and sequencing. The Falcon first stage is designed to survive atmospheric entry and to be recovered, handling both the rigors of the ascent portion of the mission and the loads of the recovery portion. Stage recoverability also provides a unique opportunity to examine recovered hardware and assess design and material selection in order to continually improve Falcon 9 and Falcon Heavy. 1.6 PRICING The standard price for Falcon 9 and Falcon Heavy launch services can be found at www.spacex.com/about/capabilities. Pricing includes range services, standard payload integration and third-party liability insurance. Please see Section 7.3 for a complete description of standard services. Nonstandard services are also available. © Space Exploration Technologies Corp. All rights reserved. 4
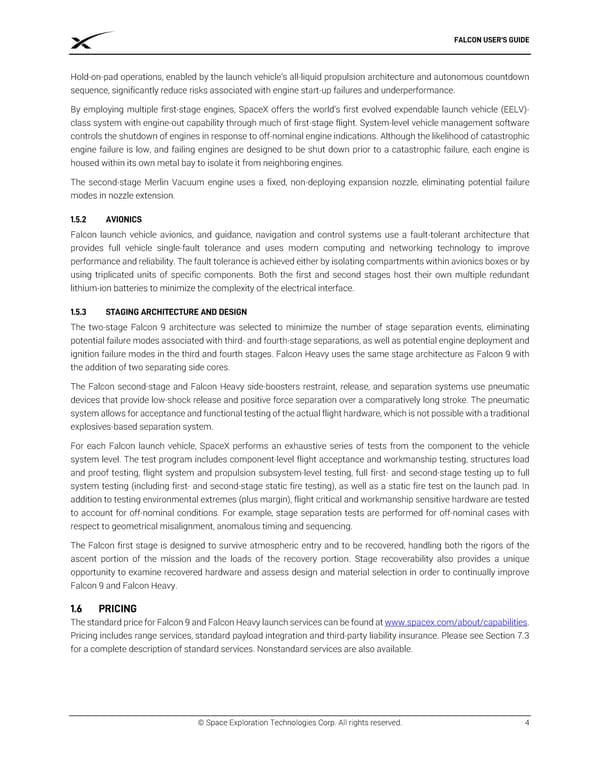